
about
adding value
to empower your products.
adding value
to empower
your products Discover more

about
engineering precision
into every design.
engineering precision
into every design Discover more

about
integrating technology
for automated excellence.
integrating
technology
for automated
excellence

about
predicting performance through
CAE Advanced Simulations.
predicting
performance
through CAE
Advanced
Simulations

about
making complexity clear
through precise documentation.
making complexity
clear through
precise
documentation
Discover more

about
transforming ideas into
Engaging Digital Experiences
transforming ideas
into Engaging
Digital Experiences
Discover more

about
turning complexity
into clear technical
animations
turning complexity
into clear
technical animations
Discover more
It's about engineering
to innovate. Together.
Since 1996.
Innovation and Engineering since 1996
Tailored Technology Solutions with Asotech
We are Asotech, and our heart beats for engineering innovation. Every day, we are dedicated to technological advancement to offer advanced engineering solutions. Our passion for new challenges and sharing our know-how with companies allows us to create innovative solutions that improve products and optimize processes, making businesses more competitive. With our expertise, we enhance your business through cutting-edge mechanical design and integrated technologies.
Case studies
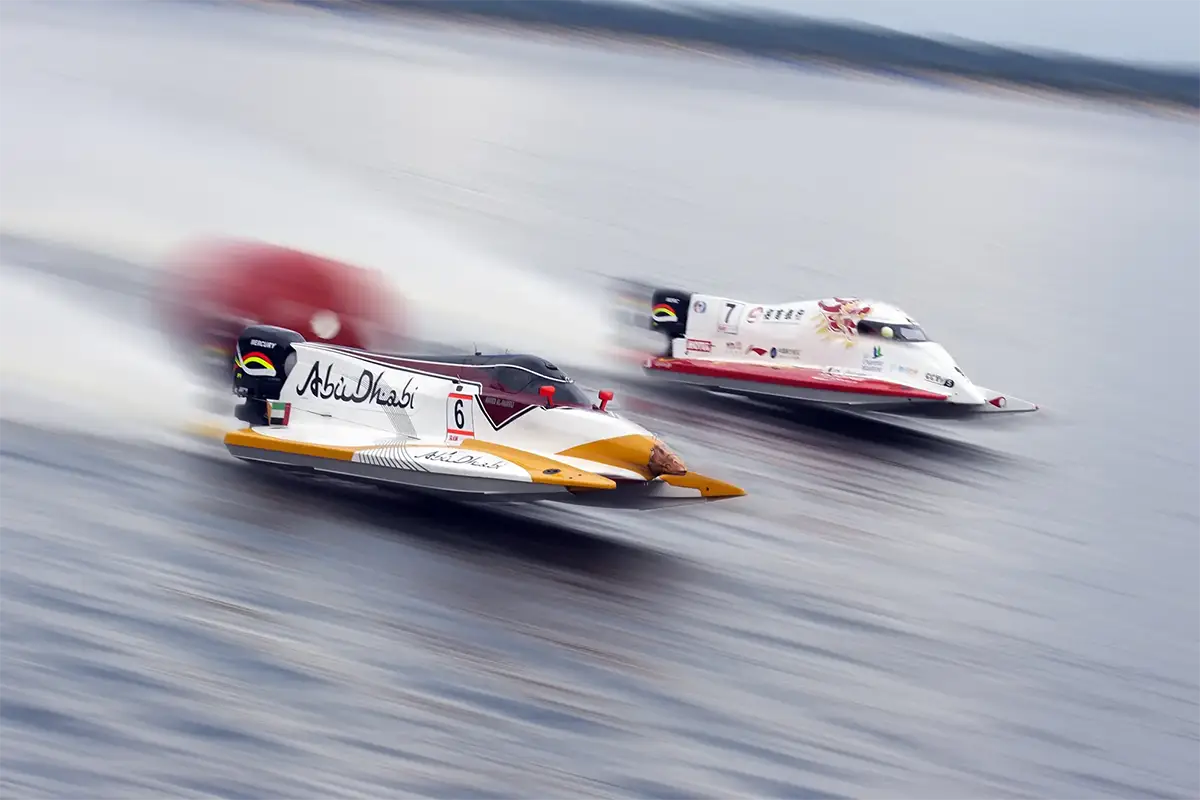
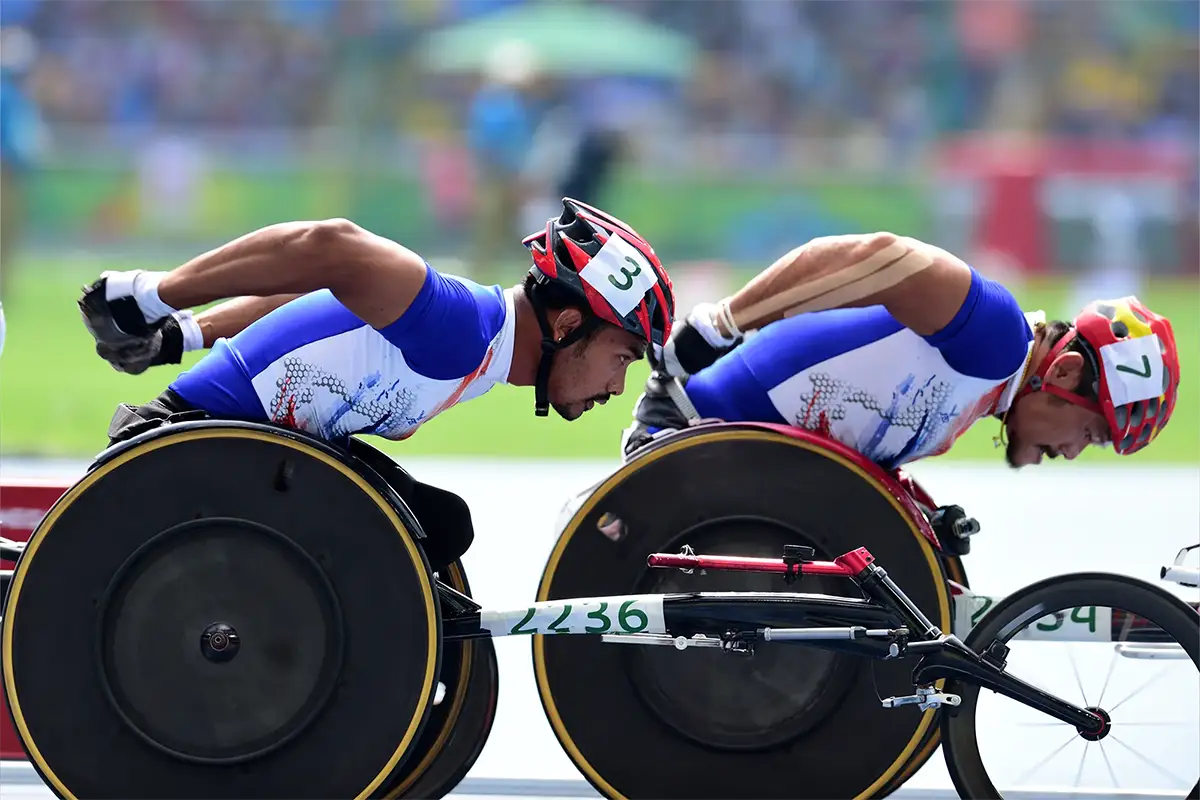
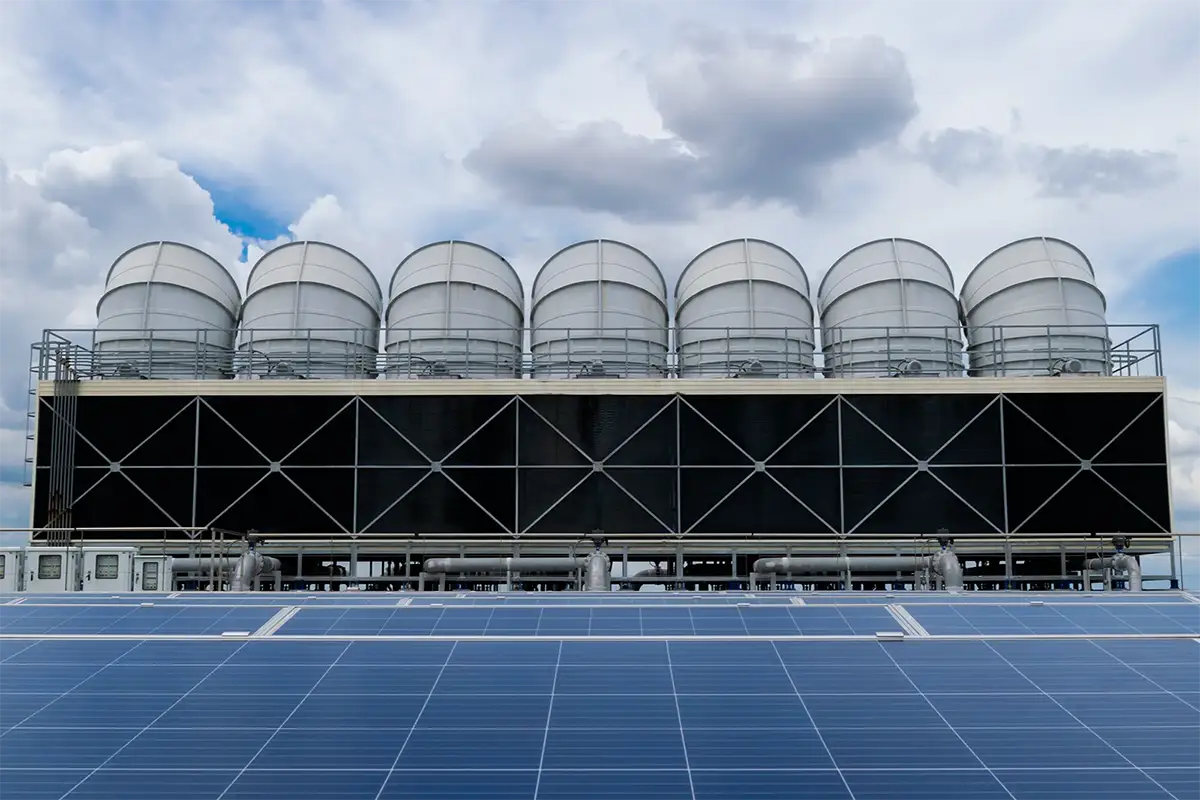
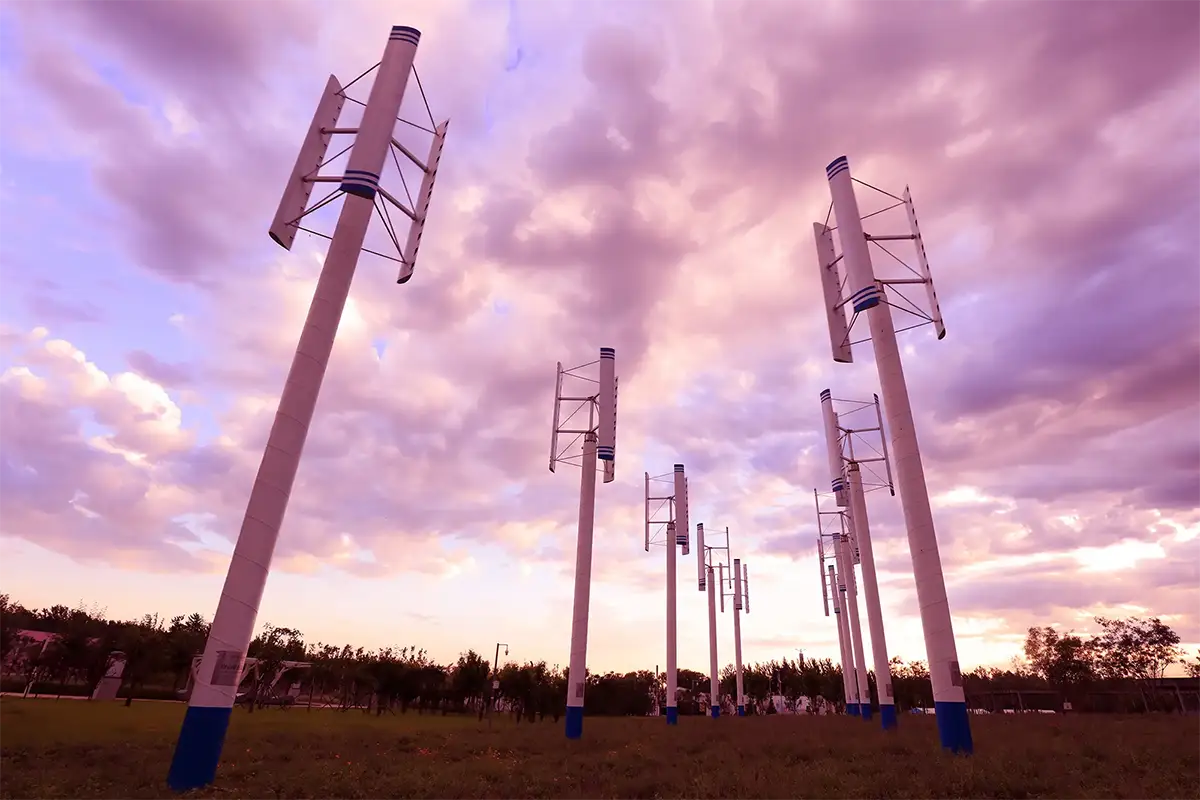
OUR OFFERING
It's
about a
total service
for complete and
integral solutions
Our multidisciplinary and transversal nature is among the capabilities that set us apart. Thanks to these, we are able to work effectively in various industrial sectors, offering a service of vertical specialization. The versatility of our staff and the variety of their skills allow us to provide integrated technological solutions, adapting to the specific needs of each project.
Explore our mechanical design services, advanced CAE analysis and technical documentation to find out how we can improve the performance of your products. We also leverage the automation hardware and software to optimize production processes and ensure operational excellence. Discover our successful projects and how we can support your business.
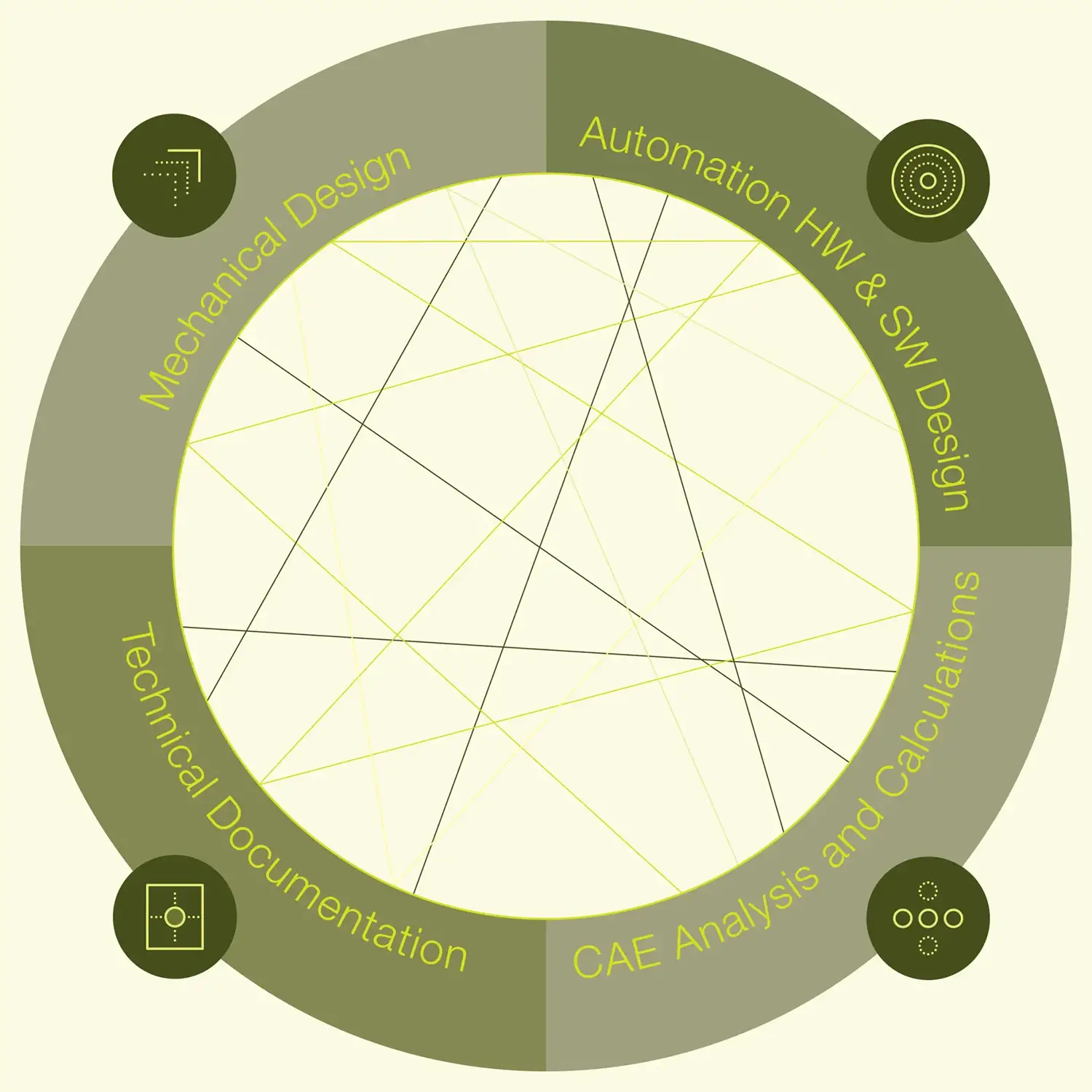
Our team
No posts were found for provided query parameters.